
Customs Clearance/Brokerage
Frequently Asked Questions
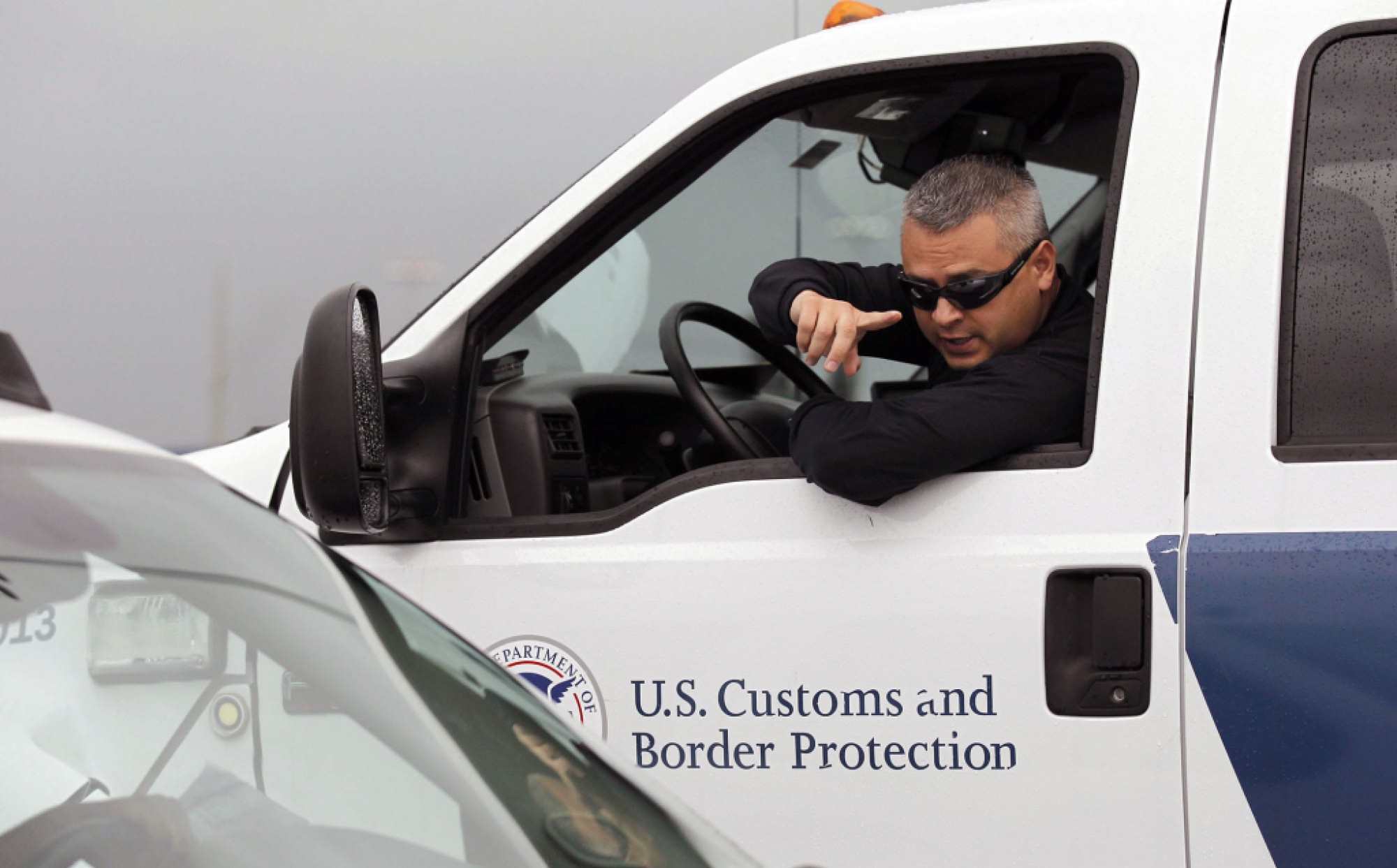
Before shipping various goods, a shipper may wonder what customs clearance means and how it’s relevant to their shipping options. Every international ocean freight shipment must meet the quota of customs clearance in each country.
Customs clearance is a necessary procedure in permitting goods that are transported to a country through an authorized customs broker. Within this process, there’s also information regarding shipments with imports and exports with parties involved in the process.
Each customs broker will have varying services and charge at different prices. Some companies choose to use a freight forwarder, which can act as a customs broker, as a result you will see a quote and contract that explains the customs elements of service.
Most customs brokers will give a client a fee that will vary based on the products that are imported, along with their value and point of origin. Typically, a record of your quote to cover items such as:
- Customs clearance charge—An admin cost that acts like a flat fee
- For sea freight consolidated shipments—Expect to see third party document, handover and various fees
- Inspection fees by government agency’s
- Necessary delivery costs
- Any agency fees or bank transfer fees
Some customs brokers offer a flat fee but it’s important that you read the fine print or added extras that can affect your final fee.
Typically, customs clearance takes less than 24 hours, however, there are times where it can take several days or weeks for goods to be inspected.
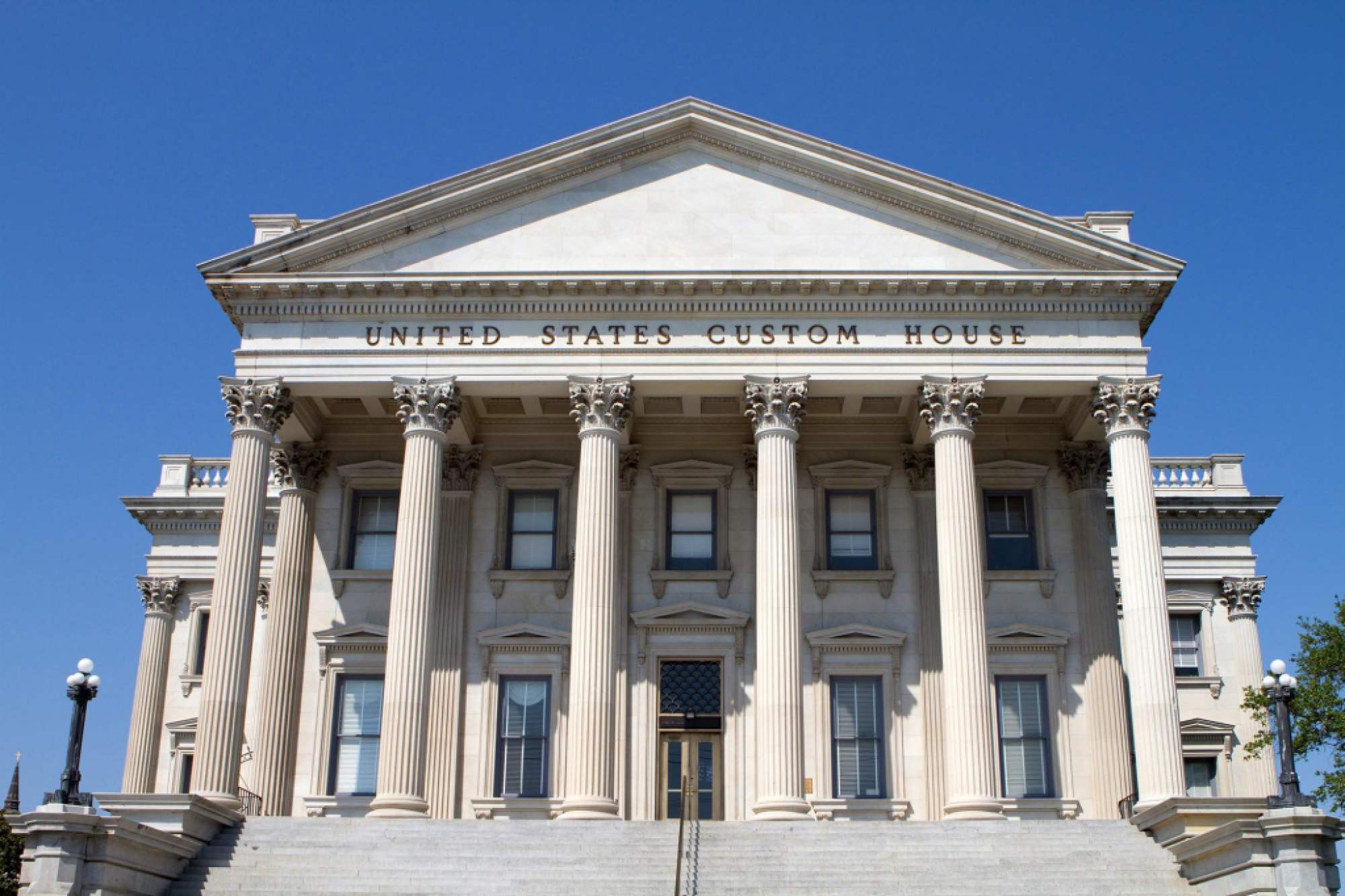
Customs clearance is necessary for all packages entering the U.S. from other countries. The U.S. Customs and Border Protection provides a form for you to complete a shipment description. This description will include a specific description of a package’s content, quantity, purchase price, the weight of an item, and the country of origin.
During the customs clearance process, it’s important that the customs declaration form is filled out correctly to avoid legal issues. Items less than $2,000 dollars do not require customs clearance.
A protection agent will prepare paperwork for importing and then release it for delivery. A package under $200 is typically cleared without additional paperwork.
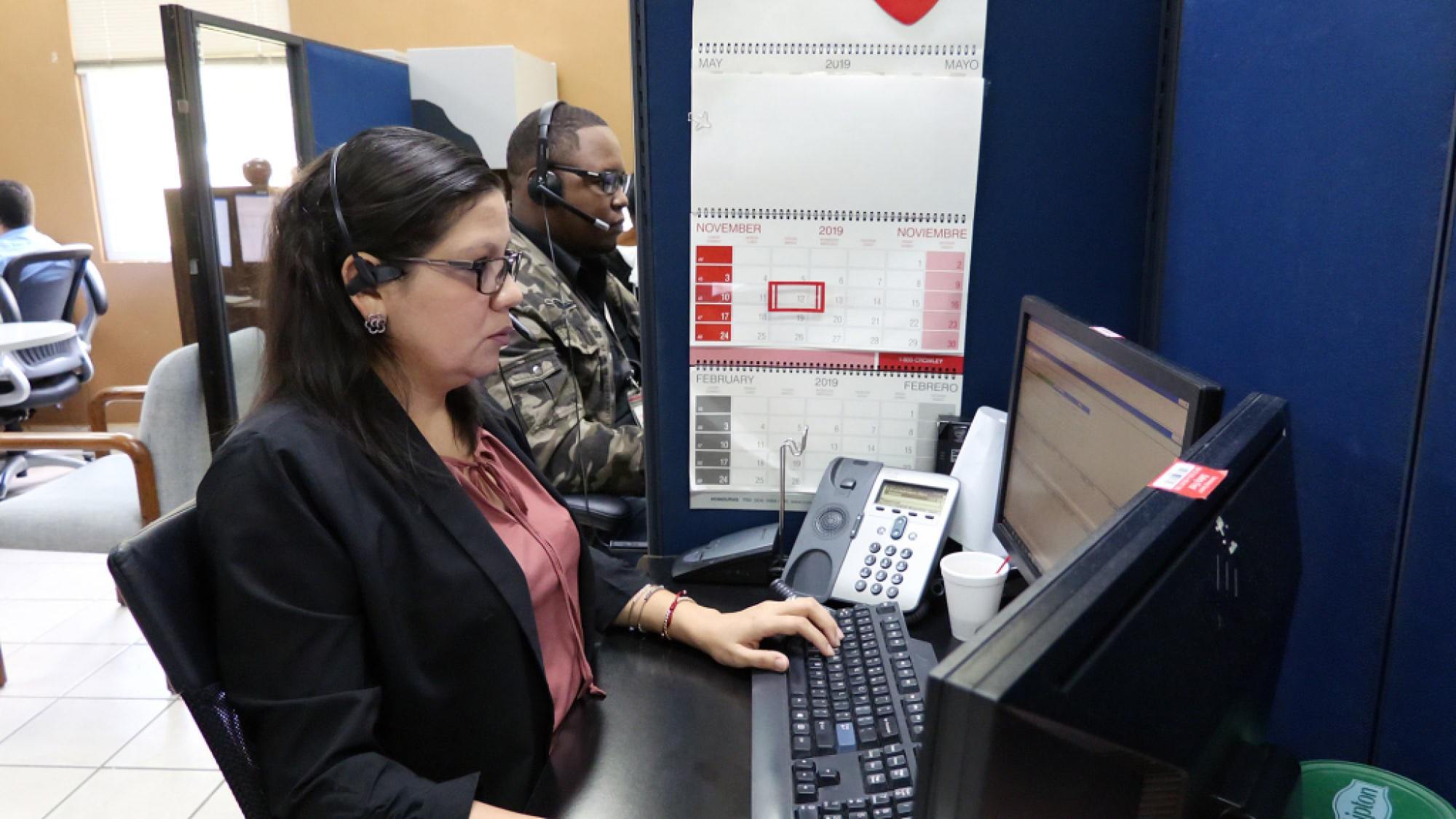
Depending on the freight forwarder, they may arrange transport logistics of a delivery and offer customs and import brokerage. As a result, you may be able to avoid multiple outsourcers.
Finding a customs broker is relatively easy to discover online. Every broker doesn’t have the ability to cover all entry points and it’s important to note if their specialty is sea ports or air freight.
Each service is offered to tailor to the specific delivery method that gives detail about importing which may generate a quote. Compare each quote that you find and check credentials of a broker before selecting one. It’s also important to check reviews from other clients.
Securing an annual bond shows Customs, and your customers that you are a serious importer and plan to continue importing to the United States. You’ll also save money by avoiding expensive single-entry bonds.
Joining the Customs-Trade Partnership Against Terrorism (C-TPAT) program expedites the release of your cargo and reduces the number of inspections, which helps aid prompt cargo availability. We encourage all of our customers to become C-TPAT certified.
When loading produce at night, insects and other pests can get inside containers more easily. This may require treatment, delays and possibly re-exporting the shipment. If you must do so at night, the use of mesh tarps during the loading process can help to reduce the risk of insects entering the container.
If you are familiar with seasonal trends, then you are better equipped to adjust your shipping volumes and patterns to take advantage of excess and restricted capacity, helping to reduce transportation costs.
Crowley Logistics’ customs clearance team advises customers to negotiate with carriers for extra time to load and unload cargo.
Using untreated wood-packaging materials violates USDA rules. When loading ocean containers or domestic trailers, ensure the treatment stamp on pallets and cartons is visible when doors are open and inspections are done. If the stamp is not visible during the inspection, your cargo will be marked for stripping. If it is not in compliance, the shipment will be re-exported or rejected.
The best way to do this is to instruct handlers to place sample boxes by the door when loading mixed commodities on a reefer. This step facilitates inspections and expedites releases, which means product spends less time in transit and more time on the store shelf.
Lack of airflow can cause thousands of dollars worth of damage to perishable shipments. Proper loading also prevents cargo from being damaged by shifting in transit. Make sure your carriers properly load cargo for airflow and secure it in the ocean container or domestic trailer.
Also, carton boxes are usually the best option because they are perforated, which allows air to flow through the boxes and reach the produce while in cold storage and inside the reefer. There’s a greater risk of experiencing potentially damaging ventilation issues when the produce is sealed or wrapped in plastic.
Crowley Logistics’ customs clearance team sends pertinent information that can affect importation of your perishable shipments via e-mail announcements to our customers. Contact us today to begin receiving important updates. You can also download a free Save Our Citrus iPhone app from the USDA by clicking here. Report your symptoms, upload a photo and receive an individual response back from citrus experts.
The use of cold-storage facilities or refrigerated warehouses, while not mandatory, has become standard in the produce exporting industry. We highly encourage this method, which brings produce to its necessary temperature, prior to its being loaded onto a reefer. Bringing the produce temperature down at this early stage, not only further stunts the aging process to secure freshness; it also helps avoid the risks of loading ‘hot’ cargo. Trying to bring down the temperature of ´hot’ cargo inside of a reefer takes longer than it does in a cold-storage type facility.
Prior to loading cargo, turn on the reefer and let it run until it reaches the needed temperature. Even if you’ve used a cold-storage facility for your cargo, it can still be susceptible to some sort of humidity if the reefer itself is not at the right temperature when everything is stored inside. To avoid thermal shock and mold, make sure to get reefer up to the needed temperature. Then, get it running with the doors closed at least 30 minutes prior to loading. This further assures the temperatures are all in line.
Refresher courses always help keep employees stay in line with business goals and best practices. This is why getting to know how reefers work and refreshing loading crews on the best practices that come with using them can be very beneficial. It helps create a more streamlined and seamless process when everyone is in line with the best practices for ensuring cargo is protected from the day it’s picked until the day it hits store shelves.